Алмазний диск – що це таке?
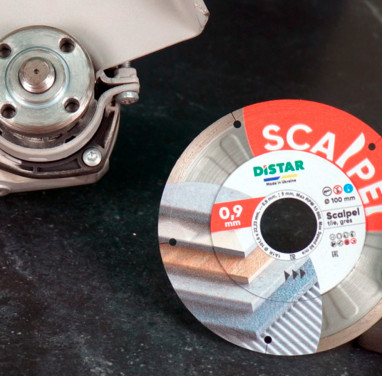
Деякі люди, почувши термін алмазний диск, відразу уявляють собі інструмент, виготовлений із рідкісного природного мінералу – алмазу. Однак це уявлення не зовсім відповідає дійсності. Давайте детальніше розглянемо конструкцію алмазного диска, адже це дуже цікава і захоплююча тема.
Як виглядає алмазний диск?
Ймовірно, більшість читачів у своєму житті стикалися з алмазними інструментами. Але якщо ви не знаєте, як виглядає алмазний диск, вас може здивувати той факт, що він не блищить, як діамант, а є звичайним сталевим кругом, по краях якого можна помітити дрібні вкраплення синтетичних алмазів.
Залежно від типу обладнання, для якого вони призначені, алмазні диски можуть мати різні розміри – від маленьких, які легко вмістяться навіть у кишені для монет у вашому гаманці (від 50 мм), до величезних дисків, більших за людський зріст (до 3000 мм).
На сталевому корпусі дисків можна знайти наклейку або позначення, нанесене УФ-друком, яке містить безліч корисної інформації, зокрема:
- Діаметр диска та монтажного отвору,
- Тип матеріалу, для якого він призначений,
- Піктограми сумісних пристроїв,
- Піктограми режиму роботи (сухе різання чи різання з водою),
- Максимально допустима швидкість обертання,
- Напрямок обертання диска.
Тепер, коли ви знаєте, як виглядає алмазний диск, можемо перейти до питання: з чого він виготовлений?
Конструкція алмазного диска
Алмазні диски складаються з кількох ключових елементів, кожен з яких має певні фізичні властивості і виготовлений із матеріалів різної твердості. Це дозволяє отримати різні ріжучі характеристики диска, що дає змогу адаптувати його до конкретного будівельного матеріалу.
Синтетичний алмаз
Алмаз є одним із найтвердіших мінералів у природі, завдяки чому він може різати майже будь-який будівельний матеріал. У виробництві алмазних інструментів використовуються виключно синтетичні алмази, оскільки це значно дешевше, ніж застосування природного мінералу. Завдяки процесу синтезу вдалося отримати алмази дуже високої твердості, які за міцністю майже не поступаються природним.
У різних дисках використовуються алмази різної твердості, що забезпечує максимальну ефективність при обробці конкретного матеріалу. Окрім самої твердості, на ріжучі властивості впливає також покриття алмазів, яке підвищує їхню зносостійкість і покращує міцність закріплення в ріжучому шарі диска. Алмази можуть бути без покриття або вкриті тонким шаром металів, таких як титан, нікель тощо. Покриті алмази мають підвищену стійкість до стирання і краще утримуються на ріжучій кромці диска навіть при високих навантаженнях і перегріві інструменту.
Корпус диска
Корпус диска має вигляд сталевого круга (суцільного або сегментованого). У його центрі знаходиться монтажний отвір. Діаметр корпусу залежить від типу обладнання, для якого диск призначений, наприклад:
- Кутова шліфувальна машина,
- Плиткоріз,
- Каменеріз,
- Швонарізчик,
- Стінорізна пила тощо.
Діаметр монтажного отвору також адаптований до типу пристрою. Наприклад, у дисках для кутових шліфувальних машин найчастіше використовується отвір діаметром 22,23 мм, який підходить до стандартного затискного фланця.
Найважливішим елементом корпусу є якість сталі, з якої він виготовлений. Деякі диски, призначені для різання м'яких і абразивних матеріалів, можуть бути виготовлені з м'якої і дешевшої сталі. Натомість диски для різання твердих матеріалів, наприклад залізобетону, вимагають використання більш міцної, а інколи навіть загартованої сталі.
Важливим параметром є також товщина корпусу. Чим більша товщина, тим більшої потужності обладнання потрібно для різання. Товщина диска також впливає на точність різу. Наприклад, для різання кераміки і керамограніту професіонали часто вибирають тонкі диски (товщиною не більше 1 мм), оскільки вони забезпечують чистий і точний різ. Для різання бетону, навпаки, використовуються товстіші диски, які здатні витримувати високі навантаження і високу температуру.
Металева порошкова суміш
Коли ми вже маємо сталевий корпус і синтетичний алмаз, виникає питання – як надійно закріпити алмази на поверхні диска? У більшості випадків для цього використовується метод порошкової металургії. Алмази змішують із різними металевими порошками (наприклад, залізо, мідь, бронза, олово, нікель, хром, вольфрам, кобальт тощо), після чого цю суміш пресують і спікають на сталевому корпусі при високій температурі (понад 800°C), іноді під додатковим тиском.
Тип використаних порошків дає змогу регулювати твердість алмазного шару диска, що є важливим фактором під час різання матеріалів з різною твердістю та абразивністю.
Окрім методу порошкового спікання, застосовуються й інші технології закріплення алмазів на диску – вакуумне спікання та гальванічне осадження. Однак інструменти, виготовлені за цими технологіями, мають значно коротший термін служби, ніж диски, виготовлені методом порошкового спікання. Це пов’язано з тим, що у вакуумних і гальванічних технологіях алмази закріплюються лише в одному шарі, тоді як у порошковому спіканні таких шарів може бути кілька.